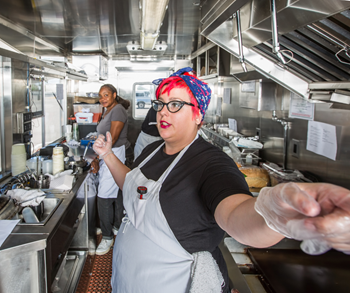
Case Study: Safety Equipment? Or Safety Hazard?
A wise person once said that the only good injury claim is the claim that never happens.
Every day, the proper use and placement of safety equipment or basic personal protective equipment (PPE) prevents many injuries and ailments. But, what happens if the equipment designed to protect and prevent injuries is the proximate cause of a work-related injury?
During new program implementations and new claims consulting, PartnerSource often works with our clients’ safety consultants and resources to maximize loss prevention impact and liability defenses. One of the many things we stress is on the importance of proper use and application of safety equipment. PartnerSource has earned the experience of knowing that unique challenges are presented if employees are misusing PPE or safety equipment on a “preventable” work injury.
Take, for example, the case of a 61-year-old employee working in a kitchen who reportedly tripped on a rubber textured fatigue mat that was stacked on top of another fatigue mat.
This employee fractured both of her ankles: she was diagnosed with lower extremity fractures with a non-displaced left ankle fracture and a trimalleolar, comminuted fracture to her right ankle requiring emergency surgery with hardware to stabilize the fracture.
The PartnerSource plan covered top-tier medical care, including inpatient rehabilitation and IV antibiotics to treat a post-surgical infection that, unfortunately, had colonized on the surgical hardware. Following a full year of rehabilitation, wound care and treatment, the employee achieved maximum rehabilitative capacity with reported permanent impairment and gait restrictions.
How Did This Happen?
At this point, you may be asking: How does an employee fracture BOTH ankles in a same-level fall? The employee provided a plausible answer related to the unique work area: 1) A food timer was going off alerting her to take a hot dish out of the oven (she was hurrying) and 2) due to the active cooking area with hot surfaces and hot food, the employee indicates she could not “catch herself” for fear of spilling hot food or contacting a hot oven surface that could cause severe burns.
Very importantly, the recorded statement taken by the adjuster confirmed details of the work area captured in post-accident pictures. The reported event matched the details of the work area. However, from the outset of the claim, the injured worker complained about the mat stacking.
Despite receiving the best available medical care and full wage replacement benefits, this employee retained competent counsel and pursued a claim of negligence based on the “mat stacking” issue and an alleged lack of response to her complaints. The adjuster did a commendable job on the recorded statement of painting a picture of a “reasonably” safe work area, to the point of achieving tepid or cautious agreement from the employee. Pictures of the work area confirmed the location of the mat stacking in a high-traffic work area near cooking equipment.
LIBS Potential
It’s important to note that this employee’s case could have Lifetime Income Benefits (LIBS) potential if it had occurred in the Texas Workers’ Compensation system, due to a diagnosis of complex regional pain syndrome (CRPS) in her lower extremities. PartnerSource is aware of a statutory workers’ compensation case with lower-extremity CRPS where a jury awarded LIBS to a claimant. CRPS – sometimes referred to as reflex sympathetic dystrophy (RSD) is a diagnosis commonly noted in negligence liability large loss and verdicts over $1 million. These facts highlight the severity of an injury that can occur from a same-level fall.
In the final analysis, this case was competently investigated, confirming a true accident with real damages, likely caused by a piece of PPE designed to PREVENT injuries. Defense counsel confirms the irony of this fact, and the sited OSHA sections 1910.22 from the plaintiff attorney prohibiting overlapping trip hazards would have been very difficult to defend on liability if the case had proceeded to arbitration or state courts.
Decades of experience in the industry affords PartnerSource unique perspective that it shares with clients. One piece of advice PartnerSource offers is to compel risk managers and safety managers to check their operations for basic proper use of safety, loss prevention and PPE. Check common preventive safety equipment, PPE, and written policies for updates, adequacy, proper use, and application – and respond promptly to employee complaints regarding safety equipment.
Avoid These ‘Safety Hazards’
Some common safety hazards to review can include:
- Worn or old rain mats in high traffic entrance or exits (“If it doesn’t lay flat, it’s not a good mat”)
- Stacked fatigue mats or other equipment used in multiples where one only should be used
- Company maintenance altering machine or saw guarding
- Improper use of work gloves (“Leather Work Gloves = Good for protecting hands from blisters…VERY INADEQUATE for protecting hands from a box cutter!”)
- Ill-fitting PPE (“Loose leather work gloves + conveyor belts or belt saws = lost digits”)
- Velcro lumbar back braces – these have been debunked as a back injury prevention device, and should not be “required” equipment in current written policies, so make sure it’s optional or at the employee’s request
PartnerSource recommends that everyone using safety equipment uses it in the most correct way to avoid it turning into safety hazards. Stay safe out there, folks!